Ultrasonic cleaning is defined as a high-precision scrubbing action to dislodge ingrained dirt and grime from the surface of sensitive items that are inaccessible and are hard to clean by hand or brushes.
Being fitted in an ultrasonic cleaning device, these Ultrasonic transducers operate on a set level of frequency generated by an oscillating diaphragm.
The cavitation process thus developed inside the machine pulls off all the stubborn soiled particles from the filthy material.
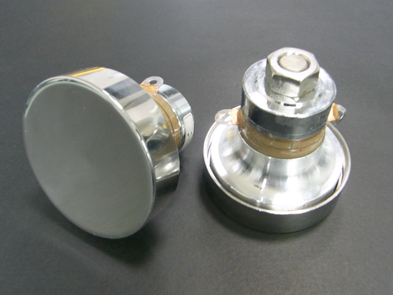
Ultrasonic transducers for cleaning are basically of two types – Magnetostrictive and Piezoelectric.
The transducers are held to an ultrasonic diaphragm which radiates frequencies and functions based on the system’s electrical efficiency.
The efficiency of the cleaning action may be a function of the constitution of both transducers.
Magnetostrictive ones are fundamentally electromagnets constructed of alloy or heavy nickel core with wire wrapped around it.
The pulsing of electrical current via the wires induces vibration in the core at a frequency that is equivalent to the ultrasonic generator’s output frequency. This concurrence of frequencies brings about cleaning action inside the tank.
Piezoelectric variants are made up of titanate and lead zirconate.
Titanate is a proven piezoelectric alloy that exhibits expansion and contraction when subjected to voltage and electrical frequency at an appropriate level.
The cleaning tank experiences ultrasonic action when vibration is induced in the ultrasonic diaphragm by the rapid expansions and contractions of the ultrasonic cleaning transducer.
Ultrasonic Transducer for Cleaning: How Does it Work?
The efficaciousness of cleaning action is further determined by the bonding method of transducers and the electrical efficiency of the system.
Piezoelectric variants are held to the diaphragm with a metallurgic bond made up of a threaded and welded stud and a high-temperature epoxy.
Magnetostrictive ones employ vacuum soldering to bond the diaphragm with the transducer’s base.
The vacuum-brazed ultrasonic transducers for cleaning have an edge above the epoxy-bonded counterpart.
The latter is highly vulnerable to an extremely abusive environment which can be characterized by the dropping of objects onto the diaphragm bringing about damage to the bond. However, transducers have been fortified against any such abuse.
Ultrasonic cleaning occurs when ultrasonic cavitation is produced in the cleansing fluid by the conversion of electrical energy into mechanical vibrations.
Piezoelectric transducers are highly efficient in converting almost the entire electrical current into mechanical vibrations, and most transducers are constructed of this one.
Magnetostrictive ones owing to the bulky size of the generator, have an energy efficiency of 50-60% only and may also call for air-conditioning to optimally maintain the temperature within.
The frequencies also play a vital role in determining the nature of the object to be cleaned through ultrasonic cleaning.
Low frequencies are deployed to clean cumbersome parts randomly, which suffer from heavy contamination, and they give rise to uneven cleaning action inside the tank.
Higher frequencies are responsible for the effective and evenly distributed cleansing action. Such frequencies possess the capability to thrash away dirt from minute blind holes, threaded regions, and other manually inaccessible regions.
The sound produced from the tank in ultrasonic transducers for cleaning will depend upon the strength and intensity of the operating frequency. Loud, audible noises can however be muffled by providing acoustic insulation for the reduction in decibel levels.